In many cities and villages across India, people often face problems like water leakage, pipeline bursts, and frequent repair work. These problems not only waste water and money but also damage roads, homes, and farmlands. Most of the time, the reason behind these failures is poor pipe jointing.
While good-quality HDPE pipes are widely used today for water supply, gas transport, and irrigation, their performance highly depends on how they are joined. If joints are weak, the entire pipeline becomes unreliable, just like a strong chain breaking at its weakest link. That’s why choosing the right pipe jointing method is very important for building safe and long-lasting infrastructure.
This article explores two key techniques for joining HDPE pipes: the conventional butt fusion method and the more advanced Electrofusion fittings process. We will explore how they work, their pros and cons, and which one offers better performance and safety for modern infrastructure projects.
What Is an HDPE Pipe Joint?
HDPE pipes are widely valued for their durability, flexibility, chemical resistance, and extended service life. But HDPE pipes are not useful unless they are properly joined. The two most popular methods of HDPE jointing are:
- Butt fusion jointing
- Electrofusion fittings
Both aim to create a strong, leak-proof connection between pipe sections, but they use different processes.
Traditional HDPE Joint: Butt Fusion Method
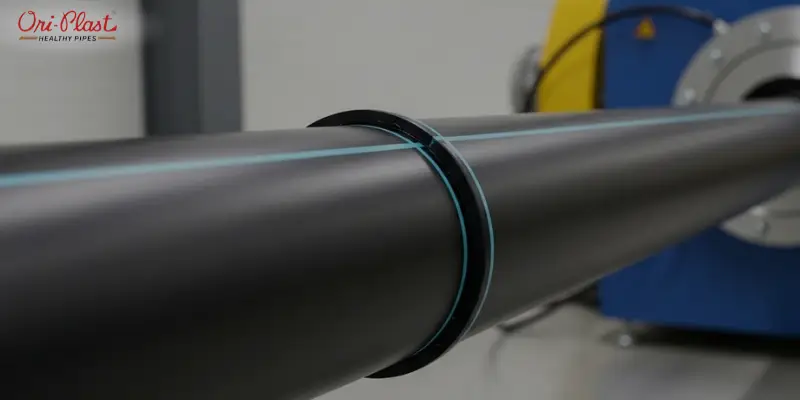
How Does It Work?
In butt fusion, both ends of two HDPE pipes are heated using a hot plate. Once they become soft and molten, the plate is removed, and the ends are pressed together. After cooling, the two pipes become one continuous piece. This is a common method for large projects with long straight runs.
Socket fusion is similar but is mostly used for smaller pipes and fittings.
Advantages of Butt Fusion
- Cost-effective for large pipelines: Ideal for long-distance water or gas pipelines where straight runs are needed.
- When performed correctly, both methods create a seamless, single-piece joint that matches the strength of the original pipe.
- Tried and tested method: This approach has been used for many years in industries such as water supply and gas distribution.
- Good for trenchless work: Works well when pipes need to be pulled underground without digging, such as in HDD (Horizontal Directional Drilling) or directional drilling.
Disadvantages of Butt Fusion
Despite its popularity, butt fusion has several challenges:
- Depends on operator skill: A small mistake in heating or pressure can create a weak joint.
- Affected by weather: Wind, dust, or rain can interfere with the fusion process.
- Needs proper space: Large butt fusion machines require open space, which is difficult in tight areas.
- Time-consuming preparation: Cutting, cleaning, and aligning must be perfect.
- Risk of joint failure: Misalignment or improper temperature may cause leaks later.
- Poor traceability: It's hard to track the quality of each joint since most records are manual.
Modern Solution: Electrofusion HDPE Pipe Fittings
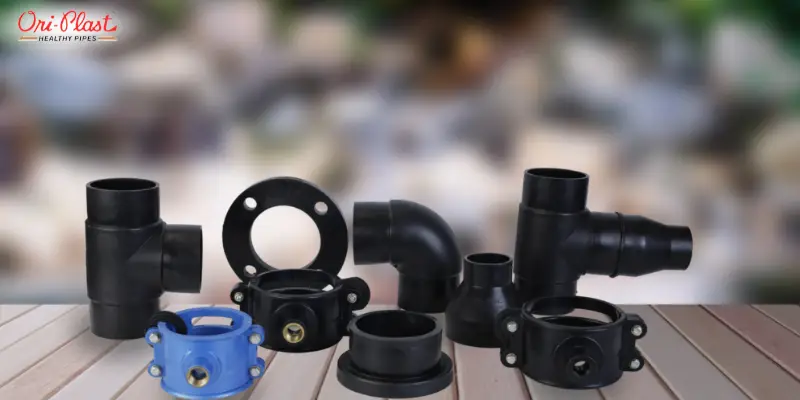
How Does It Work?
Electrofusion HDPE Pipe fittings are specially designed couplers, elbows, tees, and saddles with built-in electrical resistance wires. The pipe ends are carefully cleaned and precisely inserted into the fusion fitting to ensure a secure and leak-proof connection. An electrofusion machine passes electric current through the wires, heating the fitting from the inside. This melts the fitting and pipe surface, fusing them. After cooling, they form a strong and leak-proof bond.
Oriplast provides a wide range of electrofusion HDPE Pipe fittings made from top-quality PE100 material, suitable for potable water, gas, and industrial pipelines.
Why Electrofusion HDPE Pipe Fittings Are a Better Choice
1. Stronger and More Reliable Joints
Electrofusion creates a consistent, monolithic joint that is often stronger than the pipe itself. Since the process is controlled by machines, there is less room for human error.
2. Automatic and Accurate
The electrofusion machine reads a barcode on the fitting to set exact parameters like time and temperature. This reduces the need for guesswork and improves quality.
3. Works Well in Tight Spaces
Unlike butt fusion, electrofusion HDPE fittings can be used in small trenches, crowded urban areas, or near buildings. It’s ideal for places where large machines can’t fit.
4. Safe and Clean Process
No open flames are used. The process is safe for workers and clean for the environment. It also produces less noise and smoke.
5. Better for Repairs and Maintenance
Electrofusion is perfect for repair work on existing lines, as it doesn’t need large machines or digging. It’s also faster for installing branches and connections in complex pipe networks.
6. Long-Term Cost Saving
Even though electrofusion fittings may cost more upfront, they reduce future repair costs, water loss, and labor time. This makes them more economical over the long run.
7. Traceability and Quality Check
Each joint can be recorded using digital data. It also aids in quality control and documentation, ensuring each connection complies with industry standards during inspections and audits.
8. Corrosion-Resistant and Leak-Proof
The fusion process creates a joint that is just as corrosion-resistant as the rest of the HDPE pipe. This reliability is especially crucial in applications like underground installations and chemical transport systems.
A Simple Comparison Table
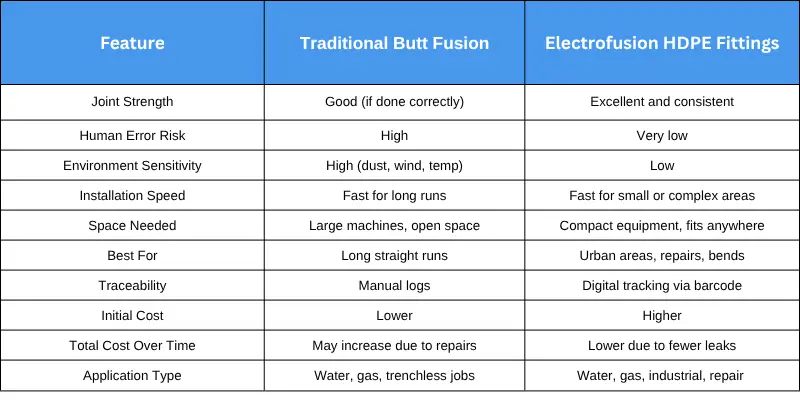
Oriplast’s Role in Better Pipe Infrastructure
At Oriplast, we understand the importance of building durable and safe infrastructure—whether it's for irrigation, municipal water, industrial pipelines, or gas distribution. For over five decades, we have delivered high-quality HDPE pipe systems and fittings that meet both Indian and international standards.
Our WRAS-certified electrofusion fittings are approved for drinking water applications. These fittings are made using safe, non-toxic materials and go through strict quality checks. From HDPE electrofusion couplers to tees, reducers, and tapping saddles, we ensure you get the best solution for your project.
Oriplast also provides guidance on machine usage, fitting selection, and operator training to help contractors and engineers complete projects efficiently.
Real-World Benefit: A Human-Centered Example
Imagine a small town where pipeline leaks happen frequently. The local government decides to upgrade their water system using HDPE pipes and electrofusion fittings from Oriplast. Within a year, complaints drop by over 70%, water supply becomes regular, and road digging due to leaks becomes almost zero. The citizens, especially women and children who earlier waited hours for water tankers, now get water directly in their homes every morning.
This is the real value of modern technology—it improves daily life. Behind every electrofusion joint, there’s a smoother routine for a family, better farming for a village, or a safer gas supply to a kitchen.
Conclusion: Choosing Technology with Trust
While both butt fusion and electrofusion offer effective solutions for joining HDPE pipes, the ideal choice depends on the specific project requirements and environmental conditions. Butt fusion may be suitable for big, open projects with long straight runs. But for most modern needs—where space is tight, quality is critical, and human lives depend on safe infrastructure—electrofusion fittings are the better, smarter, and safer choice.
They provide not just stronger joints, but also faster installations, lower maintenance, and long-term savings. Most importantly, they help build infrastructure that people can depend on—day after day, year after year.
At Oriplast, we believe infrastructure should do more than connect pipes. It should connect lives with reliability, safety, and trust. Choose Oriplast’s HDPE electrofusion fittings and ensure your next project stands strong for decades to come.
Frequently Asked Questions (FAQs)
How do electrofusion and butt fusion differ in joining HDPE pipes?
Electrofusion uses special fittings with built-in wires to heat and join the pipe ends, while butt fusion joins pipe ends by heating them directly and pressing them together. Electrofusion gives better joint quality and is easier to use in tight or complex spaces.
Which method is more reliable for underground HDPE pipelines?
Electrofusion HDPE Pipe fittings are more reliable for underground use because they offer consistent, leak-proof joints and are less affected by dust, moisture, or weather during installation.
Is electrofusion more expensive than butt fusion?
Yes, the initial cost of electrofusion HDPE Pipe fittings is higher. However, they reduce future maintenance, water loss, and repair costs—making them more cost-effective in the long run.
Can electrofusion HDPE Pipe fittings be used for gas pipelines?
Yes. Electrofusion HDPE Pipe fittings are commonly used for gas pipeline systems due to their strong, safe, and pressure-resistant joints. Oriplast also provides WRAS-certified fittings for potable water and gas lines.
What kind of equipment is required for electrofusion installation?
You will need an electrofusion welding machine, pipe scrapers for surface cleaning, and barcode scanners (if your fittings support them). Oriplast guides equipment and proper training.
Is electrofusion suitable for repair work?
Yes, electrofusion is ideal for pipe repairs, especially in urban areas or confined spaces. Electrofusion typically needs less excavation and uses more compact equipment compared to the butt fusion process.
How long does an electrofusion joint last?
When installed properly, an electrofusion joint can last as long as the HDPE pipe itself—often 50 years or more—without needing maintenance.
What is the advantage of using WRAS-certified electrofusion fittings?
Electrofusion fittings with WRAS certification are verified to be safe for potable water systems. This certification confirms that the fittings are non-toxic, rigorously tested, and compliant with international health and safety regulations.